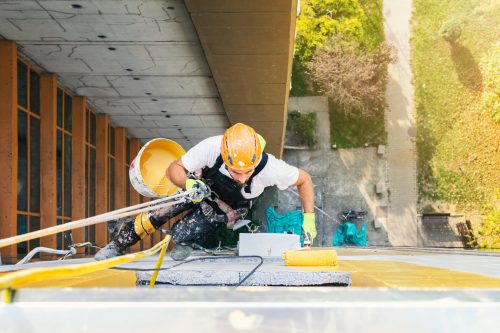
Workplace safety is a key aspect of any working environment. From offices to construction sites, getting the right workplace training for employees is essential to ensure a safe worksite. In some cases, this may include specific training on the use of equipment. In other cases, it might mean orienting employees on how to safely complete their tasks.
No matter what type of workplace safety training is required, comprehensive instruction is paramount. This means covering all aspects of safety in a clear and concise manner. Employees must be aware of common risks on workplace safety, how to avoid and minimise such safety risks, and know of any specific safety signs present in their workplace.
This article will detail the above, and – importantly – explain why such training is so very important.
Common Worksite Safety Risks
Whether they’re obvious or not, work health and safety risks can have varying levels of danger from mild injury to being life-threatening. It’s important to know the danger signs in your workplace, and here are some common ones to look out for.
- Faulty Worksite Safety Equipment – If equipment designed to keep workers safe isn’t properly maintained for long periods of time, it can lead to risks popping up if the equipment fails. From plant machinery, to agricultural equipment and everything in between, different equipment presents different risks, but any faulty equipment should not be present on a worksite.
- Falling From Heights – Work that needs to be performed from a high elevation comes with the risk of falling from heights. These risks vary in severity depending on the worksite.
- Hazardous Materials and Chemicals – Some worksites require the use and application of materials and chemicals that can be harmful to workers. Such risks can be related to physical contact or airborne inhalation.
- Fire and Smoke – Work environments that involve gases or lots of sparks, there comes a risk of accidental fires. These fires in turn can create risks of smoke inhalation – especially if smoke gets trapped.
How to Avoid and Minimise Worksite Safety Risks
Newly discovered and known risks alike both need to be mitigated as best as possible to avoid harming workers. This means finding a way to minimise said risks should be a priority. Some methods of avoiding safety risks in the workplace include:
- Acquire and Properly Maintain Safety Equipment – There is a lot of different safety equipment for worksites. Forklifts, fire alarms, and scaffolding are all present to prevent various accidents from happening or to alert workers of a dangerous situation.
- Make Sure Workers are Wearing the Appropriate Gear – When dealing with a chemical hazard or hazardous condition, workers may need to wear protective gear. This can be as simple as gloves and masks, or it can be full PPE (personal protective equipment) if the situation calls for it.
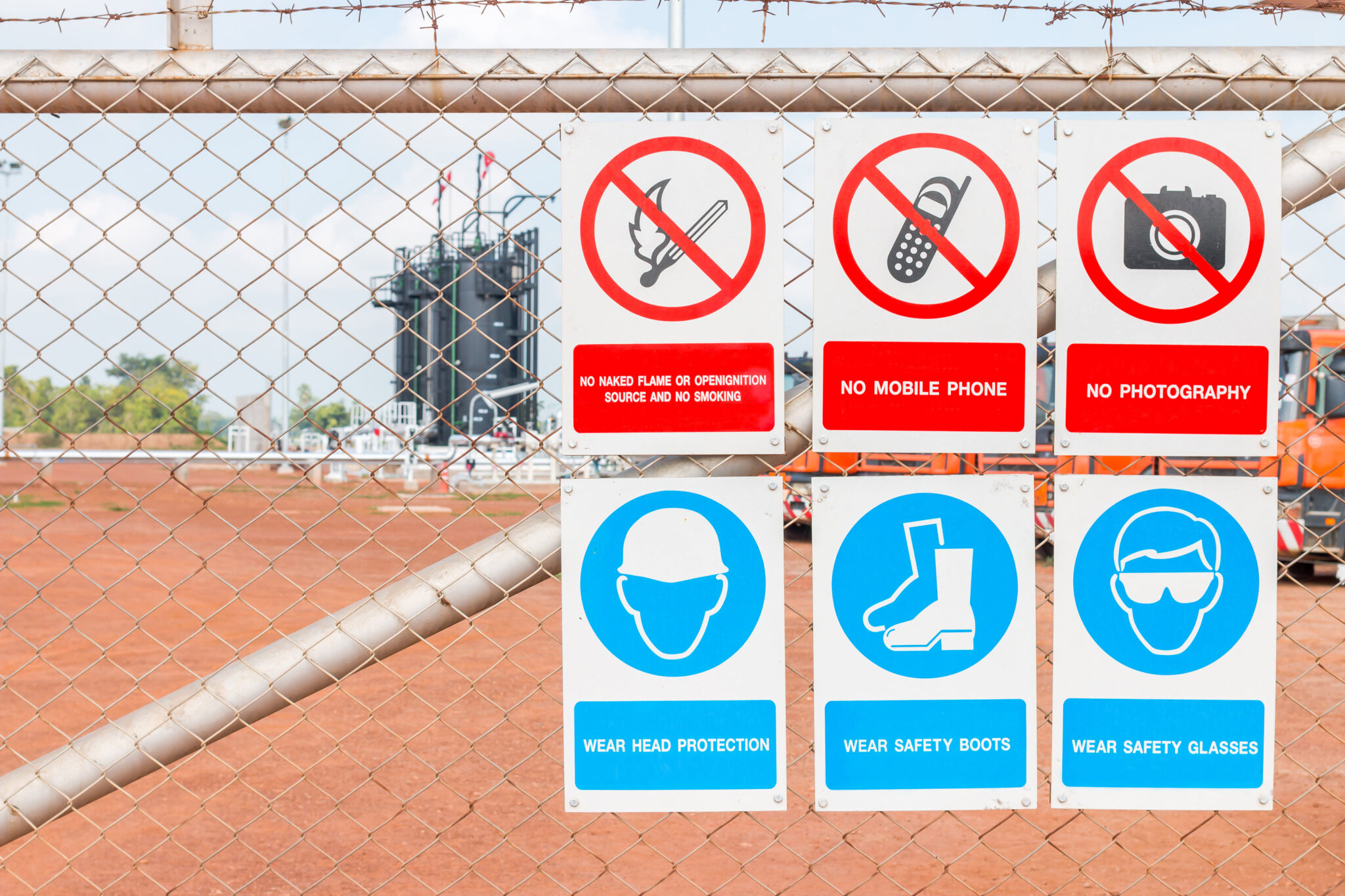
Worksite Safety Signs and Their Meanings
Worksites have a lot of different operations happening at multiple times – which means different areas will have different work health and safety risks. In these situations, getting some safety signs intended to easily display risks and/or required equipment for entry is good practice.
Here we have listed some Australian workplace safety signs and meanings:
- Mandatory Area Signs – Mandatory signs are placed to notify people that certain criteria must be met to enter the area. In most situations, this sign tells workers they need to wear some form of protective gear.
- Prohibition Signs – These signs tell people they can’t do something in an area. This can be stopping people from running through the area, or simply barring entry for anyone except authorised personnel.
- Warning Signs – When a potential occupational health risk is present that isn’t necessarily life-threatening, a warning sign is usually used. “Slippery When Wet” signs fall into this category.
- Danger Signs – Warning of a very dangerous life-threatening risk is done with danger signs. Using big bold lettering, these signs can be seen in places such as high voltage fencing.
- Informative Signs – As part of the health and safety requirements of some businesses, informative signs are placed to direct people to safety kits and equipment. These include automated external defibrillator signs and fire extinguisher signs.
The Importance of Comprehensive Training for Worksite Safety
Due to the amount of time, effort, and resources required to provide full comprehensive training to employees, business owners can sometimes be too overwhelmed to properly provide the training.
Even so, it is of utmost importance to get both new and existing workers the training they require as the benefits of doing so are wide-reaching for employees, employers, and the company as a whole.
By getting workers trained to follow proper procedures when performing tasks in potentially dangerous situations – such as operating heavy equipment – there will be fewer incidents. That in turn will mean a reduction in compensations an employer may have to make and personal leave required to be taken for the employee, while also raising confidence and morale across the whole team.
Get Worksite Safety Training from Statewide Bearings
With over 45 years of experience, we know a thing or two about worksite safety and the training required to have a fully functioning team. On top of providing quality bearings to Western Australia, we offer a wide range of additional services – including nationally accredited training programs.
Want to find out more? Contact our team today to get your workplace safety optimised.