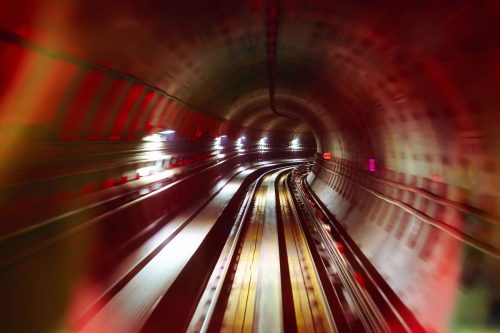
Tunnelling is pivotal in modern infrastructure, from transport systems to energy pipelines. A critical technology in these projects is the Tunnel Boring Machine (TBM), which can efficiently excavate tunnels through various geological formations.
At the heart of a TBM’s functionality are the bearings, essential components that ensure the machine operates smoothly and reliably. Without high-performance bearings, TBMs would face increased downtime, costly repairs, and inefficiencies. In this blog, we’ll explore how TBMs work, the role of bearings, and their significance in successful tunnelling operations.
What is tunnelling?
Tunnelling creates underground passages for transport systems like trains or cars, utility networks, or even pedestrian walkways. It’s an engineering feat that requires precision, advanced machinery, and careful planning.
Tunnels are essential in modern infrastructure as they allow us to build through mountains, under rivers, and in urban areas without disturbing the surface.
The relevance of tunnelling in construction and engineering cannot be overstated. It allows cities to expand without sacrificing valuable land, reduces travel times, and facilitates the movement of water, electricity, and telecommunications without disrupting the environment. To make these ambitious projects possible, tunnel boring machines (TBMs) are the tool of choice.
Examples of tunnel construction
Tunnelling involves creating underground pathways for various purposes, such as roads, railways, or pipelines. This process is essential for:
- Urban infrastructure: Reducing surface disruption by constructing underground systems.
- Utility connections: Providing a safe, concealed passage for water, gas, and electrical lines.
- Long-distance travel: Enabling high-speed rail networks and underground roads alleviating surface traffic.
Tunnelling is used globally to connect cities, create subway systems, and improve urban planning. It’s one of the most efficient ways to build infrastructure without interrupting surface activities.
How does a tunnel-boring machine work?
A Tunnel Boring Machine (TBM) is a powerful tool for digging tunnels through soil, rock, and other materials.
Here’s an overview of how a tunnel-boring machine works:
- Cutterhead: The front of the TBM, which cuts through the ground. It is equipped with various cutting tools depending on the material being bored.
- Main drive: Powers the rotation of the cutter head, allowing it to dig into the material.
Conveyor system: Transports excavated material out of the tunnel. - Bearings: Crucial for supporting the rotation of the cutter head and ensuring efficient cutting. They reduce friction and allow for smooth movement under extreme pressures.
Bearings play a critical role in this process. The main bearing supports the heavy loads during boring, ensuring smooth and efficient operation, even in harsh conditions. Without these, the machine would break down more often and lose precision.
Tunnel excavation process with a TBM: Step-by-step
Tunnel excavation with a TBM is a complex process that can vary depending on the ground conditions. Below is a basic overview of how a tunnel-boring machine works during the excavation process:
- Positioning: The first step involves placing the tunnel boring machine at the start of the tunnel route.
- Excavation: The TBM’s rotating head begins boring through rock, soil, or geological formations.
- Material removal: Excavated material is transported via conveyor belts for removal. Roller bearings ensure smooth and efficient operation of the conveyor chain system.
- Incremental movement: Hydraulic jacks push the machine forward after each section is bored.
- Tunnel lining installation: Precast concrete segments are installed behind the TBM to stabilise the tunnel walls as they progress.
- Precision and stability: Well-maintained bearings keep the TBM operating efficiently, reducing downtime and mechanical failure risks.
Seven bearings used in tunnelling machines
Tunnelling machines rely on several types of bearings, each serving a critical function to ensure smooth and reliable operation. Here are seven of the most important bearings used in TBMs:
1. Main bearing
The main bearing supports the cutter head and is one of the most crucial components of a TBM. It enables the cutter head to rotate and bore through the material. Given the immense pressure and loads it must withstand, the main bearing must be durable and capable of handling the intense forces involved in the tunnelling process.
2. Thrust bearings
Thrust bearings are designed to manage axial loads, which are essential for maintaining the forward movement of the TBM. These bearings prevent excessive axial forces from damaging other components, ensuring the machine functions smoothly as it bores a tunnel.
3. Slew ring bearings
Slew ring bearings are pivotal for allowing the TBM to turn and pivot during operation. They are often used in the machine’s cutting head or rotating section. Their ability to handle radial and axial loads makes slew ring bearings ideal for the turning and steering mechanisms of tunnel-boring machines.
4. Roller bearings
Roller bearings are commonly found in the conveyor systems of tunnel boring machines, which transport the excavated material out of the tunnel. Cylindrical roller bearings must withstand heavy loads while providing a smooth material transfer, ensuring efficient removal during tunnel excavation.
5. Tapered roller bearings
Tapered roller bearings are designed to handle heavy loads and are often used in the tunnel boring machines’ cutter head and drive sections. Their ability to support radial and axial loads makes taper roller bearings ideal for the high-stress environments typical in tunnelling.
6. Ball bearings
Ball bearings are used in various auxiliary systems within tunnel boring machines. They help reduce friction and support the rotational movement of smaller components, such as pumps and motors, ensuring smooth operation throughout the machine.
7. Journal bearings
Journal or plain bearings are used in rotating shafts to reduce friction and prevent metal-on-metal contact. They are especially useful in sections of the machine where constant rotation is necessary, but space is limited.
Tunnel excavation: The role of bearings in boring a tunnel
Boring a tunnel requires precision, stability, and efficient machinery. The role of bearings in this process cannot be overlooked. High-quality bearing systems allow the TBM to rotate smoothly, cut through different rock formations, and transport material without a hitch.
Without well-designed bearings, the friction in moving parts would increase, leading to rapid wear and tear, overheating, and potentially catastrophic machine failure. Bearings enable tunnel boring machines to maintain operational speed and ensure consistent excavation, even in challenging conditions.
Several major tunnelling projects, including the Crossrail project in London, have highlighted the importance of using the proper bearings. These bearings ensured the machines could continue boring a tunnel for extended periods without breakdowns, saving time and money.
Tunnelling hazards and managing risks
Tunnelling involves various risks, such as ground instability, water ingress, and equipment failure. Bearings can help mitigate many of these mechanical risks. Here’s how:
Common hazards in tunnelling:
- Ground stability issues: Shifts in the earth can cause TBMs to get stuck or damaged.
- Equipment failures: Bearing failure can lead to downtime, causing delays and increasing costs.
Managing risks with bearings:
- Regular inspections: Conduct frequent checks to ensure that bearings are functioning correctly.
- Replacement: Replace worn-out bearings before they cause operational issues.
- Preventive maintenance: Proper lubrication and maintenance extend the life of bearings, ensuring smoother operations.
Well-maintained bearings help reduce the risk of mechanical breakdowns, ensuring the tunnelling process remains safe and efficient.
Invest in high-quality bearings
Bearings are vital components in the successful operation of tunnel boring machines. They enable smooth rotation, reduce friction, and ensure continuous excavation. Whether it’s the main bearing supporting the cutter head or the roller bearings in the conveyor system, each bearing plays an important role in boring a tunnel.
By maintaining high-quality bearings, businesses can minimise tunnel hazards, improve machine efficiency, and ensure successful tunnelling projects.
For high-performance bearings designed for various applications and industries, contact Statewide Bearings today. We provide reliable bearings and power transmission products to meet your project needs.