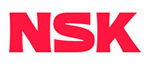
Case Study Report: Sealed Spherical Roller by NSK
Statewide Bearings in conjunction with NSK and a Pilbara WA mine site selected a conveyor pulley that had ongoing spherical bearing problems. The standard sealed spherical roller bearings were replaced with sealed spherical rollers, see the preliminary report details.
Sealed Spherical Roller Bearing (SSRB) Preliminary Condition Inspection Report
PRELIMINARY INSPECTION REPORT
Background:
NSK Sealed Spherical Roller Bearings were fitted in a pulley at a Pilbara WA Minesite, for the purpose of a trial. Pulley was installed in February 2014, as was removed in November 2014 due to an issue with the pulley lagging.
Bearings were then installed on to another pulley and put back in to service for approximately 2 years. Once again bearings were stripped from the pulley at in the presence of, Statewide Bearings and NSK personnel. Grease samples were taken and sent for analysis.
This is a preliminary inspection report, as bearings will be sent to NSK Japan for full analysis.
I have assumed that the floating and fixed bearings in the second term of service correspond to the first term of service.
Application Information:
- Application Conveyor Pulley
- Conveyor: X
- Pulley: X
- Pulley OD (new): Ø1132 mm
- Belt Speed: 5 m/s
- Pulley Speed: 59 rpm
- Bearing No. (Fixed Side): HTF320SLE316AGDD2KE4C3 (NSK – SSRB)
- Bearing No. (Free Side): HTF320SLE316AGDD2KE4C3 (NSK – SSRB)
- Radial Load: Unknown
- Lubrication: Shell ‒ Gadus S3 V220C (grease).
- Initial Grease Amount: 2240 g
- Re-greasing Amount: 70 g
- Re-greasing Frequency: 2300 hours
- Duty cycle:
- Operating Temperature: Unknown
- Fit on Shaft: h9
- Fit in Housing: H8
Observations
Fixed Side
Inner Ring Bore
Good condition. Showing multiple sleeve witness marks due to re-use. (Photo 1)
Inner Ring Raceway
Good condition with no remarkable observations. There is a distinct 360º running roller trace. Seal running trace is uniform with little wear. (Photo 2)
Outer Ring OD
Normal fretting corrosion & housing witness lines at housing split surface. (Photo 3)
Outer Ring Raceway
Good condition. Raceway has been marked; A, B, C & D at 90º intervals. The load zone depicted in Photo 8 ranges from C to D positions showing little to no wear. Several small hard particle indentations apparent at the previous inspection are still present, but have not worsened or progressed. If anything, they seem to be less visible. (Photos 4, 5, 6, 7 & 8)
Roller –
Good condition, apart from small hard particle indentations observed in previous inspection. (Photos 9 & 10)
Free Side ‒
Inner Ring Bore
Good condition. Showing multiple sleeve witness marks due to re-use. (Photo 11)
Inner Ring Raceway
Good condition with no remarkable observations. There is a distinct 360º running roller trace. Seal running trace is uniform with little wear. (Photo 12)
Outer Ring OD
Normal fretting corrosion & housing witness lines at housing split surface. (Photo 13)
Outer Ring Raceway
Good condition. Raceway has been marked; A, B, C & D at 90º intervals. The load zone depicted in Photo 18 ranges from D to A positions showing little to no wear. Several small hard particle indentations apparent at the previous inspection are still present, but have not worsened or progressed. If anything, they seem to be less visible. (Photos 14, 15, 16, 17 & 18)
Roller
Good condition, apart from small hard particle indentations observed in previous inspection. (Photo 19 & 20)
Grease Analysis:
Nine grease samples were taken ‒
- Floating housing inboard side
- Floating housing outboard side
- Floating bearing inboard side
- Floating bearing outboard side
- Fixed housing inboard side
- Fixed housing outboard side
- Fixed bearing inboard side
- Fixed bearing outboard side
- Fixed housing base. (Tested because it appeared water sitting in base of housing once bearing removed)
As expected, sample 9 had a high concentration of water. All other 8 samples registered a normal result.
Conclusion:
Both bearings are in good condition, and in my opinion would have had many more years of service. Grease analysis show that seals have been extremely effective.
The fact that indentations present since the first period of service have not progressed to flaking or spalling show that the Tough Steel™ Material that the bearing is made from has been very effective.