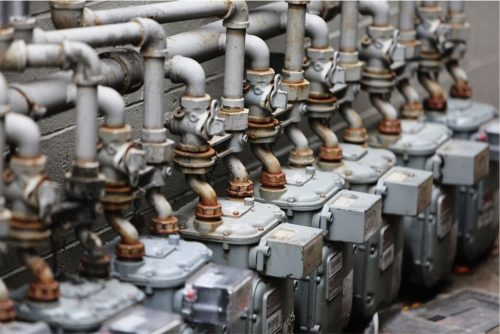
Industrial pumps are more integrated into our everyday lives than you would think. They’re essential to our standard of living but often are not thought about. Typically, they are part of larger pump systems utilised across various industries such as manufacturing, water treatment and chemical processing. Industrial pumps differ from commercial pumps as they are larger, allowing them to transport larger volumes of material such as air, gas or liquid.
Getting to know industrial pump solutions
There are many different types of industrial pumps, making it essential to understand which is right for you and your business. These pumps are categorised into two groups: dynamic pumps & positive displacement pumps.
Our pump products suit all slurry applications including chemical, mineral processing, power generation and general industry.
Dynamic pump solutions
Dynamic pumps are different from positive displacement pumps as they use a propeller/impeller to pump liquid/air/gas continuously. They are much more common than positive displacement pumps because they are less complex and can work continuously.
Centrifugal pumps
By far, centrifugal pumps are the most common type of dynamic pump. They are unique as they push material from the centre outwards through the propeller/impeller, typically low viscosity liquid such as water, etc.
These pumps are used for various applications, including water treatment plants, as they can continuously transfer large quantities of liquid. They are also used in beverage production, specifically juices, separating the solid from the liquid.
We offer spare parts needed for your centrifugal pumps to perform efficiently.
Submersible pumps
Submersible pumps work similarly to centrifugal pumps because they can be submerged in water and still operate. Typically, you would pair the two pumps to work together, with the submersible pump moving liquid out of the source of liquid and the centrifugal pump being connected to the submersible pump to move it to the surface.
These pumps are needed for emergency water removal services such as house flooding, as well as maintenance services like sewage removal. While they’re less common than centrifugal pumps, they are still important.
What are some advantages and disadvantages of dynamic pumps?
There are several advantages to using dynamic pumps, including:
- Constant flow: As mentioned, dynamic pumps can pump material constantly, necessary for pump systems like fire hydrants.
- Basic design with low maintenance: Dynamic pump designs are often quite simple with few parts, making them easier to understand and requiring less maintenance.
- Ability to transfer larger volumes: These pumps are best when large amounts of material need to be moved compared to other types of pumps.
Even with advantages, some disadvantages make positive displacement pumps better:
- Lack of high-pressure application: These pumps cannot handle high pressure and lack in comparison to positive displacement pumps.
- Cannot transport high viscous material: These pumps’ efficiency decreases as viscosity increases.
- Impeller/propeller damage: Even with the pump itself being a simple design, the main component of the impeller/propeller can be damaged and often needs to be serviced, repaired or replaced entirely.
Positive displacement pump solutions
Positive displacement pumps are different from dynamic pumps, as rather than using a propeller component to move material, they use air/water pressure to move the material. They are less common than dynamic pumps due to the intricacies of their design, with more maintenance needing to be conducted due to it having more parts.
We offer ball bearings relevant to keeping your positive displacement pumps working.
Piston pump
This subtype of positive displacement pump works by a piston moving back and forth inside a cylinder. As the piston pulls back, it creates suction that draws fluid in through an inlet valve. When the piston pushes forward, it forces the fluid out through an outlet valve.
Piston pumps can support different services within multiple industries, such as irrigation systems in agriculture.
Diaphragm pump
Diaphragm pumps work differently as they utilise a flexible diaphragm that moves back and forth, creating suction that discharges the material. These pumps are very useful when dealing with highly viscous materials as they are designed to handle them.
Diaphragm pumps support industrial industries with services such as chemical material transfers in chemical manufacturing.
Plunger pump
Plunger pumps are very similar to piston pumps but are designed for higher pressure flows.
These pumps vary in application but are typically used for high-pressure power pump washing in the oil and gas industry.
What are some advantages and disadvantages of positive displacement pumps?
Some advantages of these pumps include:
- Predictable material flow: Due to the volume of material passing through being reasonably low, it becomes simpler to calculate the total flow over a period of time based on the speed at which it’s moving.
- Longer durability: Compared to dynamic pumps, these pumps operate at a lower speed, meaning there is less stress on the pump’s mechanics.
- Ability to handle viscous material: Viscous materials work more efficiently in these pumps than lower viscous materials, as it can generate a higher pressure and flow.
However, some disadvantages would make dynamic pumps more ideal:
- Regular maintenance: These pump models are more intricate than dynamic pumps, so more parts need to be serviced regularly. This can be difficult in general due to the dangerous material passing through these pumps, making it unsafe to service them.
- Limited flow: Compared to dynamic pumps, the flow volume is relatively limited, generally because of the internal design of these pumps, especially if you’re looking to transport viscous material.
- Not economically feasible: If you don’t work with high viscosity materials, these pumps are less economically feasible than dynamic pumps.
Pump solutions going forward
If you feel more knowledgeable about industrial pumps but are unsure who can supply you or who can help with your installation, contact Statewide Bearings today to assist you with your industrial pump journey.
Our engineers have assisted existing and new customers on site with anything from design to general recommendations and advice.
No matter where you are in your industrial pump journey, we offer free, tailored and professional advice, allowing you to get the practical solutions you need. Get in contact with us today to find out more.