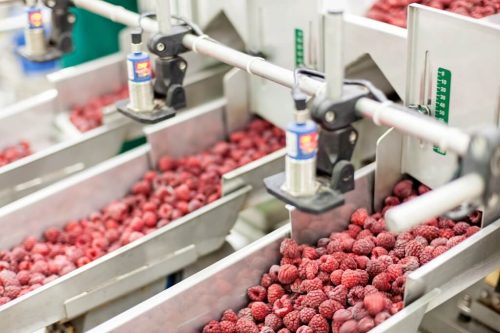
Food processing is essential for transforming raw ingredients into safe, nutritious, enjoyable food products using various machines and equipment. However, the food processing process has unique challenges, impacting efficiency, hygiene, and equipment reliability.
This article explores six significant challenges and practical solutions for overcoming them, ensuring smooth operations in the food processing industry.
Key challenges in the food processing process
1. Maintaining hygiene standards
Hygiene is critical in food processing to ensure consumer safety and comply with stringent regulations.
Ensuring that food ingredients are handled carefully and in compliance with hygiene standards is crucial to prevent contamination.
Contamination risks, such as microbial growth and cross-contact, can compromise product quality and lead to recalls.
- Regulatory requirements: Food processors must adhere to strict guidelines, using food-grade lubricant and equipment that meet industry standards.
- Impact on equipment: Poor hygiene practices can lead to equipment corrosion and increased maintenance needs.
2. Equipment wear and tear
Frequent use of food processing equipment can result in breakdowns, downtime, and costly repairs. High-pressure cleaning, heat exposure, and intensive workloads contribute to wear and tear.
- The role of food-grade grease: High-quality, non-toxic food-grade grease and lubricants help reduce friction, extend equipment lifespan, and prevent failures during production.
3. Contamination risks
Contamination is a significant concern for food processors. Greased bearings, gearboxes, and other components can leak lubricants, compromising product safety.
- Solution: Transitioning to grease-free solutions like PacFlange units, which eliminate the need for conventional lubricants ensures zero contamination and a maintenance-free process.
4. Temperature extremes
Food processing often involves extreme temperature conditions that can impact machinery performance. Standard lubricants may break down, causing equipment inefficiencies or failures.
- High-temperature lubricants: Specialised lubricants designed for high or low temperatures protect equipment and maintain operational efficiency under extreme conditions. Alternatively, grease-free solutions are also built to withstand such environments.
5. High maintenance costs
Equipment downtime and frequent replacements can significantly inflate operational costs. The food processing process requires proactive maintenance to minimise these expenses.
- Preventive maintenance: Regular checks and timely lubrication of equipment like ball bearings and spherical roller bearings can prevent costly breakdowns and extend the life of machinery.
6. Sustainability
The growing demand for sustainable practices in the food processing industry adds pressure to reduce waste and improve resource efficiency.
- Eco-friendly solutions: Using self-lubricating, corrosion-resistant materials like PacFlange units and other sustainable bearing solutions, as well as adopting renewable energy-powered machinery, can help processors meet sustainability goals.
Solutions to overcome these challenges
1. Food-grade grease and lubricants
Food-grade lubricants are vital in reducing wear, maintaining hygiene, and ensuring compliance with industry standards.
These lubricants are suitable for various applications, including blending, cooking, and cutting, ensuring safe incidental contact with food.
These lubricants are non-toxic, safe for incidental food contact, and engineered to withstand the harsh cleaning and environmental conditions typical in food processing.
2. Investing in quality food processing equipment
Durable, easy-to-maintain machinery is essential for long-term efficiency. Investing in equipment from reputable brands ensures reliability and access to a wide range of spare parts and servicing options. Features to look for include:
- Corrosion resistance: Prevents damage during high-pressure cleaning.
- Ease of cleaning: Reduces downtime while maintaining hygiene standards.
- Self-lubricating bearings: Minimises maintenance and eliminates contamination risks.
3. Preventive maintenance practices
A proactive maintenance schedule helps identify early signs of wear and reduces unplanned downtime. For instance, meat processing equipment like slicers and grinders require regular maintenance to ensure hygiene and efficiency. Key practices include:
- Inspecting bearings and other critical components regularly.
- Using advanced monitoring tools to detect potential issues.
- Ensure all workers are properly trained in operating and working with heavy equipment.
4. Sustainable practices
Modern food processors are increasingly adopting sustainable practices to meet global standards:
- Switching to energy-efficient equipment to reduce power consumption.
- Using recyclable and biodegradable materials in production processes.
5. Innovative equipment design
Equipment like PacFlange conveyor units are designed to overcome hygiene and contamination challenges by:
- Eliminating the need for grease with self-lubricating components.
- Withstanding harsh cleaning processes, ensuring long-term reliability.
Why bearings are essential in food processing equipment
Bearings like ball bearings and spherical roller bearings are fundamental to food processing equipment. Equipment for food processing, like sausage fillers, which are essential in meat processing, also rely on high-quality bearings for smooth operation.
They enable smooth operation under demanding conditions, supporting functions like cutting, mixing, and conveying. Properly maintained bearings reduce friction, ensure longevity, and improve overall productivity.
Moving forward in food processing
Addressing the challenges in the food processing process requires a combination of innovative equipment, high-quality food-grade lubricants, and preventive maintenance practices. Solutions like PacFlange units, which eliminate the need for grease and ensure zero contamination, exemplify how technology can overcome common issues.
At Statewide Bearings, we are committed to providing the best solutions for your food processing needs. With over 40 years of expertise and a comprehensive range of bearings and power transmission supplies, we help our customers maintain efficiency, hygiene, and sustainability.
Contact our team or visit your nearest Statewide Bearings branch for tailored advice and products designed to optimise your operations. Together, we can keep your food processing process running smoothly and safely.